Quando corretamente aplicada, a FMEA (Failure Mode and Effect Analysis ou, em português, Análise de Modo e Efeito de Falha) garante maior segurança e eficiência nos processos de produção, prevendo e reduzindo falhas que podem ocasionar prejuízos às linhas de produção.
Esse método de análise pode ajudar a gestão de manutenção industrial a compreender e antecipar possíveis problemas nos processos e a implantar ações antecipadas para solucioná-los.
Quer saber mais sobre FMEA e como aplicá-la?
Confira a seguir!
O que é FMEA?
Trata-se de uma ferramenta de gerenciamento de risco que identifica falhas potenciais dentro de um sistema ou processo e as classifica por probabilidade de ocorrência e gravidade.
Ela é utilizada para avaliar a confiabilidade de sistemas e identificar possíveis problemas em projetos, processos, produtos ou serviços.
Com a análise FMEA, é possível definir um plano para corrigir proativamente essas possíveis falhas, evitando seus efeitos negativos.
A análise ajuda a entender o que pode ser feito em caso de problemas, a reduzir as chances de que ocorram e a eliminar as causas que os originam.
Também possibilita a criação de um histórico dos equipamentos e processos baseados em experiências anteriores e, com a utilização dessas informações, ajuda a promover melhorias.
Quando bem aplicado, esse tipo de análise permite eliminar as falhas, conferindo maior confiabilidade do serviço prestado, segurança e satisfação do cliente. Para as empresas, essa ferramenta pode trazer maior retorno financeiro, pois evita a paralisação inesperada dos processos de produção.
Quais são os tipos de FMEA?
Existem diversos tipos de FMEAs, mas todos possuem o mesmo objetivo: identificar falhas que podem causar danos em potencial ou prejuízos às indústrias.
A seguir, os tipos mais comuns de FMEA:
- FMEA de produto: As falhas que podem acontecer nas especificações do produto são analisadas com foco nos componentes e nos subsistemas. Também pode ser chamada FMEA de projeto;
- FMEA de processos: Analisa as falhas no planejamento e na execução do processo para melhorá-lo;
- FMEA de sistema: Foca nas funções globais de sistemas;
- FMEA de serviço: Foca em processos de manufatura e montagem;
- FMEA de software: Foca em funções de software.
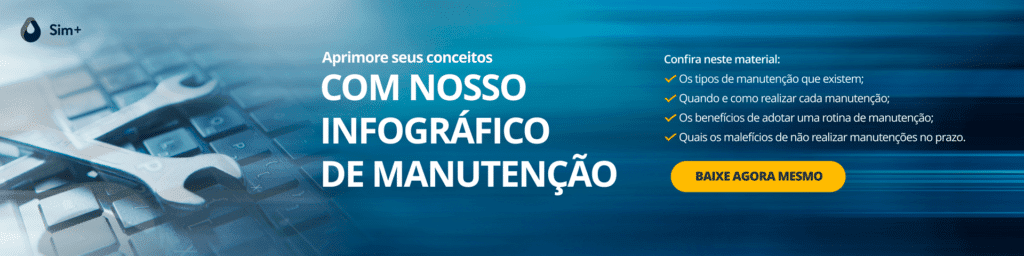
Como elaborar FMEA?
A análise FMEA envolve diversas etapas diferentes e deve ser feita por profissionais e equipes competentes, preferencialmente, experientes, multidisciplinares e com perspectivas diferentes sobre os processos ou serviços que serão avaliados.
Confira como fazer a FMEA:
Identifique as possíveis falhas
O primeiro passo é fazer uma análise geral para identificar se há ou não possíveis falhas. Portanto, verifique os processos de produção e descubra se eles estão funcionando conforme o planejado, checando se as máquinas e equipamentos estão em plena atividade.
Confira também se há alguma falha que pode impedir ou prejudicar a execução de tarefas ou afetar a qualidade dos produtos.
Observe se há algum ativo apresentando defeitos com frequência e se os operadores estão tendo problemas para executar tarefas manualmente.
Nessa etapa, é possível identificar as causas e os impactos dos problemas. É importante lembrar que um modo de falha pode ter um efeito dominó, levando a falhas em outros componentes.
Analise os riscos das falhas
Após identificar as possíveis falhas, faça uma análise cuidadosa dos riscos de cada falha, identificando se elas podem parar a linha de produção de modo não programado ou afetar a qualidade e a entrega dos produtos.
É importante avaliar todos os riscos e levantar informações para fazer um plano de ação preventivo, com a finalidade de impedir que as falhas ocorram.
Determine a gravidade das falhas
Lembre-se: há diversos níveis de gravidade entre as falhas. Portanto, é muito importante identificar o quão grave é um problema.
Assim, ficará mais fácil traçar e aplicar ações de prevenção, focando no tratamento dos ativos mais críticos em primeiro lugar.
A recomendação é fazer um ranking de falhas, deixando aquelas que acontecem mais frequentemente no topo. Isso indicará que elas são mais urgentes e que sua correção deve ser prioridade.
Para determinar a gravidade, é possível usar o sistema de classificação abaixo:
- Falhas sem efeito;
- Falhas com efeitos muito pequenos, percebidos apenas por usuários muito observadores;
- Falhas com efeito menor, com apenas uma pequena parte do sistema impactado;
- Falhas com efeito moderado, com a maioria dos usuários “incomodados” ou “irritados”;
- Falhas de efeito alto, que envolvem a perda da função primária do sistema, deixando os usuários insatisfeitos;
- Falhas com efeitos muito alto, significando que o processo, sistema ou produto se tornaram perigosos e apresentam riscos à segurança.
O próximo passo é classificar cada modo de falha pela probabilidade de ocorrência, analisando a causa raiz para determinar as causas exatas.
A classificação vai de “0” (menos prováveis) a “10” (mais prováveis). Ou seja, quanto maior for a probabilidade, mais urgente será a necessidade da correção da falha.
Coloque o plano de ação em prática
Com a classificação das falhas e o levantamento da probabilidade delas ocorrem, é possível traçar um plano de ação para impedir que elas aconteçam ou para minimizar sua frequência.
Esse plano de manutenção deve ser muito detalhado, especificando tudo o que deve ser feito e quais são os responsáveis por sua execução.
Por fim, execute o plano de ação. Todos os resultados devem ser monitorados e servirão para identificar a eficácia ou não das estratégias adotadas para correção.
Quais são as vantagens da FMEA?
- Maior conhecimento dos problemas nos processos de produção;
- Possibilidade de hierarquizar informações sobre falhas;
- Possibilidade de estabelecer sistema de prioridades de melhorias;
- Geração de um banco de informações para melhorias futuras;
- Aumento da confiabilidade, qualidade e segurança dos processos;
- Implantação da cultura de prevenção de falhas.
Conclusão
Como deu para perceber, o método de análise FMEA ajuda a aumentar a confiabilidade e a rastrear as ações para mitigar os riscos de ocorrência de falhas.
Por isso, é uma excelente ferramenta para a gestão da manutenção industrial. Para auxiliar ainda mais os gestores, a Construmarket oferece a plataforma Sim+.
Com o software, é possível reduzir o número de falhas em equipamentos, acelerar o atendimento e realizar paradas de manutenção dentro de um planejamento eficiente, colaborando assim com a produção e maximizando o tempo de vida útil de equipamentos e componentes.
LEIA TAMBÉM: